Lionel Nallet, de capitaine du XV de France à capitaine d’industrie
Proposé par Avec l’Industrie
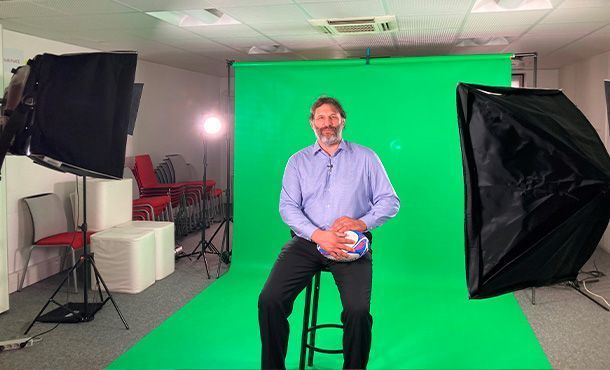
On avait quitté Lionel Nallet un soir de 2011 (ou plutôt un matin, compte tenu du décalage horaire), lors d’une finale mondiale entre la France et la Nouvelle-Zélande, à l’Eden Park d’Auckland. Il s’en était fallu de peu (d’un point très exactement) pour que les Bleus ne remportent un premier titre planétaire. L’ex-deuxième ligne est aujourd’hui à la tête d’une entreprise d’usinage industriel spécialisée dans la mécanique de haute précision. Retour sur un parcours hors du commun.
Et pour en savoir plus sur l’industrie et sur les centaines de perspectives de carrière qui s’offrent à vous, rendez-vous sur aveclindustrie.fr.
Lionel, en 2015, après l’arrêt de ta carrière, tu n’as pas été tenté de te reconvertir dans le rugby ?
Pas du tout [rires, NDLR] ! J’ai pris du plaisir en jouant, mais je ne me voyais pas entraîneur ou consultant. J’ai besoin d’être pleinement acteur. Dès 2007, j’ai monté avec mon beau-frère une entreprise d’usinage industriel en mécanique de haute précision, Usirea. Quand j’ai raccroché les crampons, je n’ai pas eu le temps de cogiter. Je me suis investi à 100 % dans l’entreprise.
L’usinage industriel, c’est très spécifique, tu as suivi une formation particulière ?
Oui, j’avais obtenu un BTS Productique avant de me consacrer pleinement au rugby. Au collège, j’étais en échec scolaire. J’avais besoin de concret, alors j’ai fait un apprentissage dans l’usinage industriel. C’est un secteur d’autant plus concret que les pièces qu’on produit, on les retrouve partout. Mon beau-frère, quant à lui, est titulaire d’une licence en mécanique.
Quelle est la mission principale d’Usirea ?
On produit des pièces métalliques de haute technicité pour nos clients. C’est vraiment du cas par cas, d’ailleurs, on ne travaille qu’en petites et moyennes séries. Nos clients sont dans des secteurs sensibles : le nucléaire, l’aéronautique, la défense. On a réalisé des pièces pour Airbus, pour la fusée Ariane ou encore pour le refroidissement de centrales nucléaires. On n’a pas vraiment le droit à l’erreur [rires].
Et concrètement, comment on fabrique ces pièces de haute technicité ?
Pour faire simple, on enlève de la matière avec des outils coupants à commandes numériques. Par exemple, on utilise des machines de tournage-fraisage cinq axes. Elles permettent, en plus des trois axes principaux, de travailler la matière sur les angles. Grâce à ces deux axes supplémentaires, on peut faire pivoter la pièce et la maintenir en position. La matière est alors usinée de manière plus complexe.
Tu as commencé ta phrase par « pour faire simple », mais j’imagine que c’est tout sauf simple…
C’est ça [rires] ! C’est un métier très technique, qui demande beaucoup de rigueur. D’ailleurs, c’est un parallèle que je fais avec le rugby. On doit en permanence adapter nos stratégies d’usinage. Ce qui est vrai pour une matière ou une pièce ne l’est pas forcément pour l’autre. En plus, on travaille au centième, voire au macro, ça demande beaucoup de sérieux pour régler les machines et contrôler leur précision. Pour maîtriser tous ces paramètres, rien ne vaut l’expérience. Je dirais qu’il faut cinq-six ans pour être complètement opérationnel.
Comment se répartissent les rôles au sein de l’usine ?
On est une vingtaine en tout. Mon beau-frère a un profil plus technique que le mien, il gère le pilotage de l’atelier et moi, les achats de matières premières, les sous-traitants, la planification et le contrôle qualité. On travaille sur plan, c’est-à-dire qu’on a un bureau des méthodes qui, à la réception d’une commande, va déterminer une stratégie d’usinage (les outils et conditions de coupe) et réaliser une simulation 3D de la pièce. Puis on lance la fabrication de la pièce avec les régleurs, qui vont programmer les machines et corriger les cotes, et les opérateurs, qui rechargent et contrôlent les machines. On contrôle la première pièce, puis on lance la série en la recontrôlant à intervalles réguliers.
On sent que le contrôle qualité est omniprésent…
C’est fondamental, oui. Les pièces qu’on réalise demandent un niveau d’exigence élevé, des contrôles tridimensionnels et géométriques. On utilise des moyens de mesure de très haute technologie, étalonnés et vérifiés très régulièrement. C’est ce qu’on appelle la métrologie. On assure aussi la traçabilité de toutes les matières premières qu’on utilise.
Quand on a été capitaine du XV de France, ça doit être une formalité de manager une usine…
Oui, c’est sûr, ça aide d’avoir passé 15 ans de sa vie en groupe. On apprend à composer avec tous les types de personnalités, à tirer le meilleur de chacun et à se rassembler autour d’un objectif commun. D’ailleurs, depuis que l’entreprise existe, on a toujours été en croissance. Ça nous permet d’investir massivement dans des machines encore plus techniques et performantes.
L’innovation technologique est incontournable dans l’industrie ?
Clairement, et ça va vite ! Quand j’ai commencé mes études, il n’y avait même pas de machines qui faisaient à la fois du tournage et du fraisage. Aujourd’hui, on a des machines de tournage-fraisage cinq axes ! Tout cela permet de proposer un cadre de travail plus agréable aux équipes.
Quel est ce cadre de travail, justement ?
On est loin du cliché de l’usine sale et bruyante. Toutes les machines sont électriques, donc peu bruyantes, et numériques, donc l’environnement de travail est très propre. Mais le cadre de travail va bien au-delà. L’objectif, c’est de garder nos salariés, leur expérience est fondamentale. On utilise la robotique pour les décharger des activités pénibles. On veille aussi à ce que la vie professionnelle n’empiète pas sur la vie privée. Les horaires sont normaux, on ne travaille pas la nuit ni le week-end. Et puis on propose beaucoup de sessions de formation. L’idée, c’est qu’un opérateur puisse évoluer en régleur, et qu’un régleur puisse rejoindre le bureau des méthodes.
Et la transition écologique dans tout ça ?
Elle est omniprésente. Quand on travaille dans l’industrie aujourd’hui, la décarbonation est un objectif majeur. À notre niveau, on utilise au maximum 5 % d’énergie fossile. Tout le reste vient de l’électricité issue du solaire et de l’éolien. La politique de recyclage est primordiale également. On trie nos métaux, on les recycle et on les revend. Et puis on ne travaille qu’avec des sous-traitants de la région. L’idée, c’est vraiment de contribuer à une économie circulaire.
Quelles sont les perspectives de développement d’Usirea ?
On aimerait se diversifier pour gérer des affaires globales avec de l’assemblage en plus de l’usinage. C’est aussi pour ça que l’évolution et la montée en compétences de nos salariés sont importantes.
Rejoindre l’industrie, c’est participer à la construction de demain. Faire partie de cette aventure, c’est avoir un impact sur le monde via des projets qui associent savoir-faire et nouvelles technologies, au service de défis comme la transition écologique.
L’industrie, c’est aussi un large éventail de carrières. En fait, c’est simple : si ça se fabrique, alors il existe un secteur de l’industrie dont c’est le métier ! De la chimie à l’aéronautique en passant par le textile, le luxe ou encore la métallurgie, l’industrie est partout. Découvrez tous les métiers de l’industrie sur aveclindustrie.fr.
Portes ouvertes, salons, rencontres… il y a forcément un événement près de chez vous. Du 27 novembre au 3 décembre 2023 c’est la semaine de l’industrie ! Retrouvez le programme sur aveclindustrie.fr